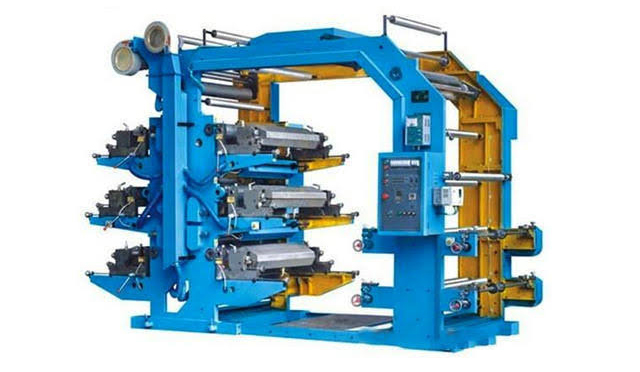
Our robustly constructed Flexographic Printing Machine has an excellent speed range of 50 -100 meter per minute most suitable for 2, 4, 6, & 8 colour for Paper, LD, Non-Woven, Woven Sacks & other Substrates. Our machine is easy to install and operate. It gives high speed with great accuracy. Our elegantly designed machine also ensures reduced wastage as it has tolerance free format. It also has reverse printing arrangements and gives uniform impression.
We are a prominent Flexo Printing Machine Manufacturer, Exporter and Supplier in India. The Range Includes Flexographic Printing Machine, Woven Bag Printing Machine, Multi Color Flexo Printing Machine, PP Woven Bag Printing Machine, Non-Woven Bag Printing Machine, HDPE Bag Printing Machine, PP Bag Printing Machine in modulate design with arched bridge Stack Type. With many years of worthy experience let this model stand out for its economic efficiency and high precision printing, flexographic printing machine as the most successful one in the world markets. Printable Materials includes PP, WOVEN, NON-WOVEN,HM, HDPE, LD, LLDPE, B.O.P.P, Polyester, Polypropylene, Foam Sheets, Paper, Aluminium Foil etc.
Our robustly constructed Flexographic Printing Machine has an excellent speed range of 50 -100 meter per minute most suitable for 2, 4, 6, & 8 colour for Paper, LD, Non-Woven, Woven Sacks & other Substrates. Our machine is easy to install and operate. It gives high speed with great accuracy. Our elegantly designed machine also ensures reduced wastage as it has tolerance free format. It also has reverse printing arrangements and gives uniform impression.
A flexographic print is made by creating a positive mirrored master of the required image as a 3D relief in a rubber or polymer material. Flexographic plates can be created with analogue and digital plate making processes in our Flexo Printing Machine. The image areas are raised above the non-image areas on the rubber or polymer plate. The ink is transferred from the ink roll which is partially immersed in the ink tank. Then it transfers to the anilox roll (or meter roll) whose texture holds a specific amount of ink since it is covered with thousands of small wells or cups that enable it to meter ink to the printing plate in a uniform thickness evenly and quickly (the number of cells per linear inch can vary according to the type of print job and the quality required). To avoid getting a final product with a smudgy or lumpy look, it must be ensured that the amount of ink on the printing plate is not excessive. This is achieved by using a metal scraper, called a doctor blade. The doctor blade removes excess ink from the anilox roller before inking the printing plate. The substrate is finally sandwiched between the plate and the impression cylinder to transfer the image. The sheet is then fed through a dryer, which allows the inks to dry before moving on. In the case a UV ink is used, the sheet does not have to be dried, but is dried from UV rays. Basic Parts of the Press Unwind and Infeed Section. The roll of stock must be held under control so the web can unwind as needed Printing Section- Single colour station including the fountain, anilox, plate and impression rolls Drying Station- High velocity heated air, specially formulated inks and an after-dryer can be used Outfeed and Rewind Section- Similar to the unwind segment, keeps web tension controlled.
Specifications:
Web Width | 300mm To 1500mm |
Speed | 50mtr. To 100mtr. |
Material | sPaper, LD, Non-Woven, Woven Sacks & other Substrates |
Heating | Electrical, Hot Air-Generator, Thermicfluid. |
Drive | Single Motor, 3Motor Synchronized Drive. |
Optional | Optional Air Shafts, Web Aligner, Ink Circulation Pump |
Enquiry Now